The Press Shop plays a vital role in automotive production, shaping the vehicle’s structural and “skin” parts through metal stamping. Errors at this stage are critical, as they are ‘carried over’ to future stages from the beginning of production, producing many anomalies and costs. So, how can we minimise human error in this critical phase?
Machine vision is a game changer
Machine Vision is a game-changer in automating quality control, eliminating reliance on manual inspections, reducing human errors, and improving production line efficiency. Systems integrated with 3D guidance ensure the correct placement of parts and dies during stamping. With cameras and 3D sensors, real-time alignment and positioning monitoring occur before stamping starts. This reduces die damage caused by misaligned parts and speeds up tool and setup changes, minimising downtime.
Have you ever wondered how minor alignment errors affect the entire vehicle assembly?
The answer is clear; this misalignment can cause a part to be NOK. This is why it is necessary to check the presence, diameter, and exact location of the bores of the structural parts. These vision systems ensure every hole match CAD specification, preventing assembly errors down the line while improving traceability by recording accurate data for each inspected part.
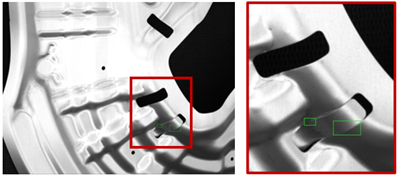
Artificial vision also uses specular lighting and high-resolution cameras to detect surface defects on the parts that will become the vehicle’s visible surfaces. Operating in real-time within the production line, these systems identify defects as they happen, ensuring only flawless parts move forward and enhancing the final vehicle’s perceived quality.
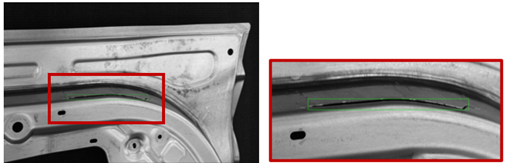
Are we overlooking the benefits of 3D vision and laser-based systems in measuring the dimensions and geometry of each stamped part? These systems identify deformations or tolerances that deviate from specifications. This reduces rework and material waste, ensuring parts are ready for perfect assembly.
Thanks to dedicated artificial vision algorithms, NOK parts are automatically detected and sorted to separate defective pieces. This guarantees that only safe, ready-to-assemble parts reach the following stages, speeding up production and removing the need for manual inspections.
What about ensuring the right material is being processed in the correct orientation? Artificial vision verifies that the material is correct, linking to management software to track parts through the line. This prevents material errors, reduces rework costs, and ensures the production line operates smoothly.
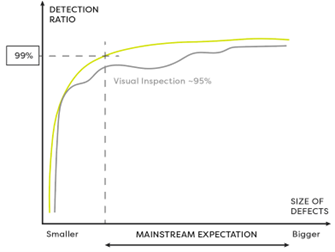
One key benefit is reducing human error. Machine vision systems work continuously and accurately, eliminating human fatigue and subjectivity.
Non-intrusive, fast inspections integrate directly into the production line, minimising disruptions
Conclusion
Isn’t it surprising how detecting defects early in the Press Shop can save costs in later stages like assembly or painting? By ensuring conforming parts from the start, customers will receive a vehicle of higher quality. Additionally, data collected by the systems helps identify trends and make real-time preventive adjustments, improving sustainability by reducing material waste and optimising energy usage.
Ultimately, artificial vision is revolutionising quality. So, is it time to trust technology to take the Press Shop to the next level?